Силы взаимодействия зубьев принято определять в полюсе зацепления. Распределенную по контактной площадке нагрузку в зацеплении заменяют равнодействующей F n , нормальной к поверхности зуба. Эту силу удобно представить в виде составляющих F t, F r , F а.
Окружная сила F t = 2 10 3 Т/d ;
Осевая сила F a = F t tgβ
На ведомом колесе направление окружной силы F t совпадает с направлением вращения, на ведущем – противоположно ему.
Радиальная сила F r = F R tgα = F t tgα / cosβ
Векторы радиальных сил у колес с внешним зацеплением направлены к оси, а у колес с внутренним зацеплением – от оси зубчатого колеса.
2. Расчет прямозубых цилиндрических передач на контактную прочность.
Контактная прочность зубьев является основным критерием большинства зубчатых передач.
В передачах без смещения a w = (d 2 ± d 1)/2 = d 1 (u ± 1)/2
Откуда d 1 = 2 a w /(u ± 1) d 2 = 2a w u/(u ± 1),
где u = d 2 /d 1 – передаточное число передачи.
Наибольшее контактное напряжение в зоне зацепления определяют по формуле Герца:
ν 1,2 – коэффициенты Пауссона материалов контактирующих тел;
Е 1,2 – модули упругости материалов;
ρ 1,2 – радиусы кривизны контактирующих поверхностей;
b – длина линии контакта (длина цилиндров)
Силу F n определяют по окружной силе с учетом коэффициента нагрузки. По результатам экспериментов для расчетов суммарную длину
b= l Σ контактных линий определяют с учетом коэффициента торцевого перекрытия: F n = K H ·Ft/cosα ; b = l Σ = 3b 2 /(4 - ε α).
Контакт зубьев рассматривают как контакт двух цилиндров с радиусами кривизны профилей зубьев в полюсе зацепления:
Подставим полученные значения в формулу Герца:
Σ(1/ρ i)
= 1/ρ 1 ±
1/ρ 2
= (ρ 2
± ρ 1)/(ρ 2 ρ 1)
=
Обозначим:
Z E
=
- коэффициент, учитывающий упругие
свойства материалов сопряженных колес;
Z E
= 191.6 МПа 0,5
для стальных колес при Е 1
= Е 2
= 2,1 10 5 МПа
и ν 1
= ν 2
= 0,3.
Z H
=
- коэффициент, учитывающий форму
сопряженных поверхностей зубьев в
полюсе зацепления; Z H
= 2.5 при α w
= 20 о.
Z ε
=
- коэффициент, учитывающий суммарную
длину контактных линий; Z ε
= 0.9 для прямозубых колес при ε α
= 1,6.
При
этом получим расчетную зависимость в
форме предусмотренной стандартом:
;
Заменив в формуле F t = 2 10 3 Т 1 /d 1 ; b 2 = ψ bа а w ; d 1 = 2а w /(u ± 1) , последовательно получим
Решив
относительно а w
получим а w
=
;
Обозначив
К а
=
Формула
проектировочного расчета цилиндрических
зубчатых передач имеет вид: а w = К а
В соответствии со стандартом:
для прямозубых передач К а = 450 МПа 1/3 ;
для косозубых и шевронных передач К а = 410 МПа 1/3 .
В целом межосевое расстояние косозубой цилиндрической зубчатой передачи примерно на 20% меньше межосевого расстояния прямозубой передачи.
При расчете цилиндрических передач значение коэффициента ширины зубчатого венца колеса ψ ва = b 2 /а w задают. В зависимости от расположения шестерни относительно опор принимают: ψ ва = 0,2 …0,5.
Формула для проверочного расчета:
Значения коэффициента Z σ для цилиндрических стальных передач:
прямозубых Z σ = 9600 МПа 1/2 ;
косозубых и шевронных Z σ = 8400 МПа 1/2
При проектировочном расчете значение коэффициента расчетной нагрузки К Н = 1,3 – задают ориентировочно. При проверочном расчете определяют его уточненное значение по известным размерам и степени точности передачи.
При выполнении проверочного расчета желательно достижение равенства σ Н = [σ] Н , так как при σ Н > [σ] Н – возможно занижение ресурса передачи, а при σ Н < [σ] Н завышение ее массы. Простейшим способом достижения σ Н = [σ] Н является изменение ширины зубчатого венца b 2 . Контактная прочность зубьев колес зависит от материала и размеров передачи и не зависит от модуля и числа зубьев в отдельности. По условиям контактной прочности при данном а w модуль и числа зубьев могут иметь различные значения, но с соблюдением условий: 0,5m(Z 1 + Z 2) = а w и u = Z 2 /Z 1 .
3.Расчет зубьев цилиндрических передач на прочность при изгибе .
Вторым из двух основных критериев работоспособности зубчатых передач является прочность зубьев при изгибе. При выводе расчетной зависимости принимают допущения:
В зацеплении находится одна пара зубьев.
Зуб рассматривают как консольную балку, нагруженную сосредоточенной силой F n , приложенной к зубу в его вершине
Сила F n действует под углом (90 – α /) к оси симметрии зуба; угол α / несколько больше угла зацепления α w . Для выявления напряженного состояния зуба силу F n переносят вдоль линииN 1 N 2 зацепления до пересечения с осью зуба в т. С. и раскладывают на составляющие, направленные вдоль оси зуба и перпендикулярно ей (рис. 2).
Под действием составляющей, направленной вдоль оси, в основании зуба действуют напряжения сжатия σ сж = F n sinα / /bS, эпюра которых показана на рис.3 (b- длина зуба). Точки А и В определяют положение опасного сечения зуба при изгибе. Зуб в этом сечении нагружен изгибающим моментом М = F n h р cosα / , вызывающим действие напряжений σ и: слева от оси – растяжения, справа – сжатия. Суммарные напряжения σ Fном со стороны растянутых волокон (т.А) имеют меньшие значения, чем со стороны сжатых (т.В). Однако напряжения растяжения являются более опасными. Напряжения, наеденные без учета концентраторов, называют номинальными.
Определим номинальные напряжения изгиба – сжатия в т.А:
где W x = bS 2 /6 - осевой момент сопротивления опасного сечения АВ.
Выразив силу F n через окружную силу F t с учетом коэффициента нагрузки K F , получим:
, где F n
= K F F t /cosα w
Опасное сечение АВ расположено в зоне концентрации напряжений, вызванной изменением формы на переходной поверхности в основании зуба. Местное напряжение в этом сечении превышают номинальные в α Т раз:
σ F = σ F ном α Т, где α Т – теоретический коэффициент концентрации напряжений.
С учетом этого напряжения в опасном сечении
Плечо изгиба h p и толщину зуба S выражают через модуль m
где
- коэффициент, учитывающий форму зуба
и концентрацию напряжений. Выбирается
по таблице или графику.
Учитывая условие прочности σ F < [σ] F , получим формулу для проверочного расчета зубчатых передач по напряжениям изгиба:
,
где Y β – коэффициент, учитывающий угол наклона зуба Y β = 1 – β/100, при условии Y β > 0.7; Yε - коэффициент, учитывающий перекрытие зубьев Y ε = 1/ε α = 1/1,6 = 0,65.
Для прямозубых зубчатых колес : Y β = 1; Y ε = 1 при степени точности 8,9;
Y ε = 0,8 при степени точности 5, 6, 7. Y FS 1 > Y FS 2 так как зуб шестерни у основания более тонкий, чем зуб колеса. Для обеспечения примерно равной изгибной прочности сопряженных зубьев шестерню изготавливают из более прочного материала. Условие равной прочности на изгиб зубьев шестерни и колеса: [σ] F 1 /Y FS 1 ~ [σ] F 2 /Y FS 2
Заменив
F t
= 2 10 3 T 1 /d 1
u
d 1
= 2a w /(u
± 1), получим формулу для проверочного
расчета зубьев по напряжениям изгиб и
решим полученное неравенство относительно
m:
Ширину b 1 венца шестерни выполняют на 2 – 4 мм больше ширины b 2 колеса для компенсации возможного осевого смещения зубчатых колес из-за неточности сборки. Это важно при приработке зубьев, когда более твердая шестерня перекрывает по ширине менее твердое колесо.
Приняв b = b 2 и обозначив K m = 10 3 Y FS Y β Y ε , получим расчетную зависимость для определения минимального значения модуля зубьев
m
,
где К m = 3.4 10 3 – для прямозубых передач;
K m = 2.8 10 3 – для косозубых передач.
Вместо [σ] F в формулу подставляют меньшее из [σ] F 1 u [σ] F 2 .
Особенности геометрии и условий работы косозубых передач
Ось червячной фрезы, при нарезании зубьев косозубой цилиндрической передачи, составляет с торцевой плоскостью колеса угол β. Поэтому в нормальной к направлению зуба плоскости все его размеры – стандартные. У косозубого колеса расстояние между зубьями можно измерить в торцевом или окружном, (t – t) и нормальном (n – n) направлениях. В первом случае получают окружной шаг p t , во втором – нормальный шаг p. Различны в этих направлениях и модули зацепления:
m t = p t /π , m n = p / π , где m t ; m n – окружной и нормальный модули.
p t = p / cosβ , следовательно, m t = m n / cosβ . Нормальный модуль должен соответствовать стандарту.
Для колеса без смещения делительный d и начальный d w диаметры:
d = d w = m t Z = m n Z / cosβ
Помимо торцевого перекрытия в косозубых передачах обеспечено и осевое перекрытие.
Коэффициент осевого перекрытия ε β = b 2 /p x , где p x - осевой шаг, равный расстоянию между одноименными точками двух смежных зубьев, измеренному в направлении оси зубчатого колеса (рис.)
Особенности геометрии определяют отличия условий работы косозубой передачи.
1. Зуб ведомого колеса входит в зацепление, начиная с вершины, вначале увеличивая, а затем уменьшая длину контактной линии при перемещении ее от головки зуба, к ножке. Зуб работает не сразу всей длиной, он лучше и быстрее прирабатывается.
2.Увеличивается время контакта одной пары зубьев, в течении которого входят в зацепление новые пары зубьев; нагрузка передает большое число контактных линий, что значительно снижает шум и динамические нагрузки. Чем больше угол наклона β линии зуба, тем выше плавность зацепления.
3.Нагрузка по длине контактной линии распределяется пропорционально суммарной жесткости зубьев шестерни и колеса.
4.В косозубой передаче в зацеплении участвуют одновременно 2-3 пары зубьев. Поэтому суммарная длина контактной линии l Σ кос больше (примерно на 30%), чем в прямозубой l Σ прям
l Σ кос = b 2 /(Z 2 ε cosβ b) ; l Σ прям = b 2 /Z 2 ε .
Коэффициент Z ε учитывает суммарную длину контактной линии:
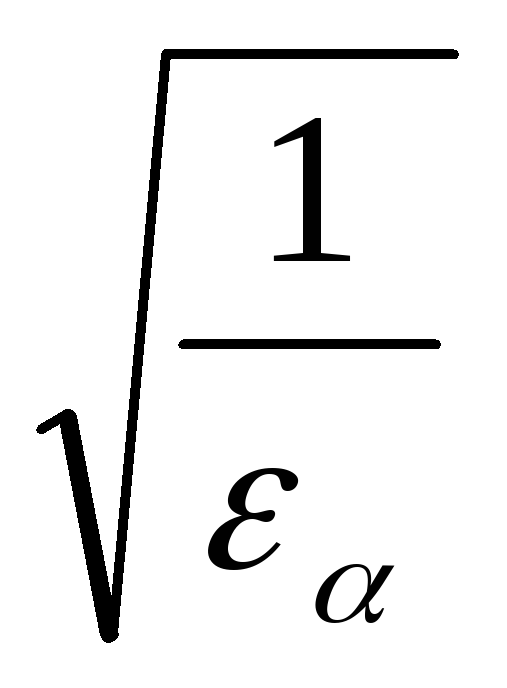
Для прямозубых передач Z ε
=
где ε α – коэффициент торцевого перекрытия.
5.Соотношение между радиусами кривизны контактирующих зубьев в косозубой передаче более благоприятно: Σ(1/ρ і) кос = cosβ b Σ(1/ρ і) прям
Контактные напряжения при прочих равных условиях в косозубом зацеплении меньше по значению, чем в прямозубом.
Понятие об эквивалентном колесе .
Профиль косого зуба в нормальном сечении n – n совпадает с профилем прямозубого колеса. Расчет косозубых колес ведут, используя параметры эквивалентного прямозубого колеса:
m n - модуль; Z v - число зубьев. Профиль зуба совпадает с профилем условного прямозубого колеса, называемого эквивалентным , делительный диаметр d v = m n Z v .
d v = 2ρ v = d/cos 2 β = m t Z/cos 2 β = m n Z/cos 3 β , где ρ v – радиус кривизны.
Из равенства m n Z v = m n Z/cos 3 βследует эквивалентное число зубьев:
Z v = Z/cos 3 β.
C увеличением угла β наклона линии зуба, эквивалентные параметры возрастают, способствуя повышению прочности передачи.
Σ(1/ρ i)
= 1/ρ 1 ±
1/ρ 2
= (ρ 2
± ρ 1)/(ρ 2 ρ 1)
=
Обозначим:
Z E
=
-
Z H
=
Z ε =
;
Заменив в формуле F t = 2 10 3 Т 1 /d 1 ; b 2 = ψ bа а w ; d 1 = 2а w /(u ± 1) , последовательно получим
Решив относительно а w получим
а w
=
;
Обозначив
К а =
а w
= К а
, где
F n
= K F F t /cosα w
h p = μm и S = λm , где μ и λ - коэффициенты, учитывающие форму зуба. Тогда
где
-
, где Y β
m
ПРОЕКТИРОВОЧНЫЙ РАСЧЕТ ЦИЛИНДРИЧЕСКОЙ ПЕРЕДАЧИ
При проектировочном расчете зубчатой передачи удобнее определять не напряжения, а основные геометрические параметры. Межосевое расстояние:
a w
= (u
+ 1)=
, мм
где u - передаточное число;
T 2 - крутящий момент на колесе;
C - коэффициент, учитывающий механические свойства сопряженных зубчатых колес:
310 – для прямозубых цилиндрических передач;
335 – для прямозубых конических передач;
270 – для косозубых цилиндрических и конических передач;
[σ] H - допускаемое контактное напряжение, зависящее от материала и термообработки зубчатых колес и от длительности работы передачи
Зубчатые колеса изготовляют из проката или поковок из качественные конструкционных углеродистых или легированных сталей с содержанием углерода от 0,1 до 9,6% с различными видами термообработки; при значительных размерах колес (диаметром более 500 мм) применяют стальное литье. У прямозубых колес из улучшенных или нормализованных сталей с твердостью не более НВ 350 твердость рабочей поверхности зуба шестерни должна быть на 20 – 50 ед.больше твердости зуба колеса. У не прямозубых колес разность в твердости шестерни и колеса достигает 100 ед.и более, что повышает нагрузочную способность передачи по контактной прочности.
При значительной, но спокойной нагрузке может быть произведена сплошная закалка, при большой и динамической нагрузке внутренняя часть зуба должна быть вязкой, а наружная высокопрочной, при малой динамической нагрузке весь зуб может быть вязким. Если передаваемая мощность большая, то для уменьшения массы и габаритов передачи следует применять колеса с более высокой поверхностной прочностью.т.е. зубья должны иметь сплошную или поверхностную закалку, цементацию, цианирование и … Такие зубья должны шлифоваться или притираться, следовательно степень точности должна быть высокой. Колеса с шевронными зубьями закалке не подвергаются и их шлифовка не производится.
Допускаемые контактные напряжения для шестерни и колеса:
где [σ] Р 0 – допускаемое контактное напряжение, соответствующее базовому числу циклов нагружения N НО (выбирается по таблице 1)
Z R – коэффициент, учитывающий шероховатость рабочих поверхностей зубьев (при 7 классе шероховатости –1; при 6 классе шероховатости – 0,95)
Z V – коэффициент, учитывающий влияние окружной скорости и твердости (определяется по графику Z V – V при твердости НВ≤ 350 и НВ > 350)
К НL
– коэффициент долговечности К Н L
=
где N HO -базовое число циклов нагружения
N HE –эквивалентное число циклов нагружения колеса
N HE
=
где Т i mах – максимальный длительно действующий момент
Т i – моменты в ступенях нагрузки, соответствующие числам циклов нагружения N i (график изменения нагрузки)
N i = 60n i t hi K K(ш)
где n i - частота вращения вала при действии момента Т i , мин -1 ;
t hi - продолжительность действия нагрузки Т i , в часах;
K K – количество зацеплений рассчитываемого колеса.
[σ] Н
=
=
После определения следует проверить выполнение условия:
[σ] Н ≤ 1,23[σ] Н min
С увеличением в сторону увеличения надежности для косозубых передач можно принять значение [σ] Н равным меньшему из двух [σ] Н1 и [σ] Н2
К Нα – коэффициент, учитывающий неравномерность распределения нагрузки между зубьями; для прямозубых колес 1; для косозубых по графику;
К Нβ – коэффициент, учитывающий неравномерность распределения нагрузки по длине контактной линии – определяется по графику или по таблице;
К НV – динамический коэффициент, учитывающий влияние точности передачи, твердости зуба и окружной скорости – определяется по таблице;
Ψ ва – коэффициент ширины зубчатого венца
Ψ ва = b/a w Ψ bd = b/d
Выбор значений ψ ba и ψ bd существенно влияет на качество передачи – ее КПД, габариты, требования к технологии изготовления и сборки; с увеличением коэффициента ширины зубчатого венца повышается концентрация нагрузки При проектировочном расчете величиной ψ ва задаются:
0,125…0,20 – для прямозубых колес коробок передач;
0,20…0,35 – для прямозубых колес редукторов;
0,20…0,50 – для косозубых колес;
0,40…0,80 – для шевронных передач.
Для каждой последующей ступени редуктора ψ ва увеличивается на 20 – 30% по сравнению с предыдущей.
Стандартные значения:0,100; 0,125; 0,160; 0,20; 0,250; 0,315; 0.40; 0,50; 0,630; 0,80; 1.0; 1,25
После определения межосевого расстояния принимают ближайшее стандартное значение: 40; 50; 63; 71; 80; 90; 100; 112; 125; 140; 160; 180; 200; 225; 250; 280; 315; 355; 400; 450; 500; 560; 630.
После корректировки параметров и коэффициентов производится проверочный расчет на контактную выносливость:
σ Н
=
МПа
Здесь в случае, если контактное напряжение не более, чем на 5 …6% превышает допустимое, или недогрузка не превышает 10% то расчет считается удовлетворительным.
Проверка на контактную прочность при кратковременных перегрузках:
σ Н max
= σ H ,
МПа
где [σ] Нпр – предельное напряжение на контактную прочность:
при Н ≤ НВ 350 [σ] Нпр = 3,1σ Т
Н > НВ 350 [σ] Нпр = 41,3НRС
Проверка на выносливость при изгибе:
σ F
=
,
МПа
где Т – крутящий момент на проверяемом колесе, Н.м.
Z – число зубьев проверяемого колеса;
К F α - коэффициент нагрузки, учитывающий распределение нагрузки между зубьями (для прямозубых колес К = 1; для косозубых при среднем коэффициенте торцевого перекрытия ε α = 1,5 и 8 степени точности колес
К Fβ - коэффициент, учитывающий неравномерность распределения нагрузки по ширине венца (таблица)
K FV - коэффициент, учитывающий динамические нагрузки (таблица)
Y F - коэффициент прочности зубьев, определяется по эквивалентному числу зубьев
Z V = Z/cos 3 β
β – угол наклона зуба в косозубых (8 0 … 20 0) и шевронных (25 0 … 40 0) передачах;
Y β - коэффициент, учитывающий наклон зуба, при β< 40 0
Y β = 1 – β/140 0
m - модуль зацепления (для косозубых m n - нормальный модуль)
m = m n = (0,01 … 0,02)a w
Модуль зуба колеса нужно выбирать минимальным так, как с его увеличением растут наружные диаметры заготовок, но не менее1,5 …2 для силовых передач
Определяем числа зубьев колес:
Z 1
=
Z 2
= uZ 1
Минимальное допустимое значение Z 1 , без риска подрезания ножки зуба, для некоррегированных колес: Z min ≥ 17cos 3 β
Допускаемое напряжение при проверочном расчете на выносливость зубьев при изгибе: [σ] F = [σ] F 0 K FL Y R Y M
где [σ] F 0 – допускаемое изгибное напряжение, соответствующее базовому числу циклов перемен напряжений N FO (таблица)
K FL – коэффициент долговечности, зависящий от соотношения базового и эквивалентного чисел циклов нагружений
K FL
=
N FO = 4 10 6 – базовое число циклов
N FE
=
- эквивалентное число циклов при изгибе
m F - степень, m F = 9 – для стальных колес с нешлифованной поверхностью при твердости НВ > 350 и для чугунных колес; m F = 6 – для колес с твердостью менее НВ350
Если N FE > N FO = 4·10 6 то принимаем K FL = 1
Y R – коэффициент, учитывающий шероховатость рабочих поверхностей (1 – для шлифованной и фрезерованной поверхностей; 1.05 – цементация, азотирование; 1,2 – полированная с нормализацией или улучшением)
Y M = 1 при d ≤ 300 – коэффициент, учитывающий диаметр колес.
Определение геометрических параметров цилиндрических колес
Диаметр делительной окружности:
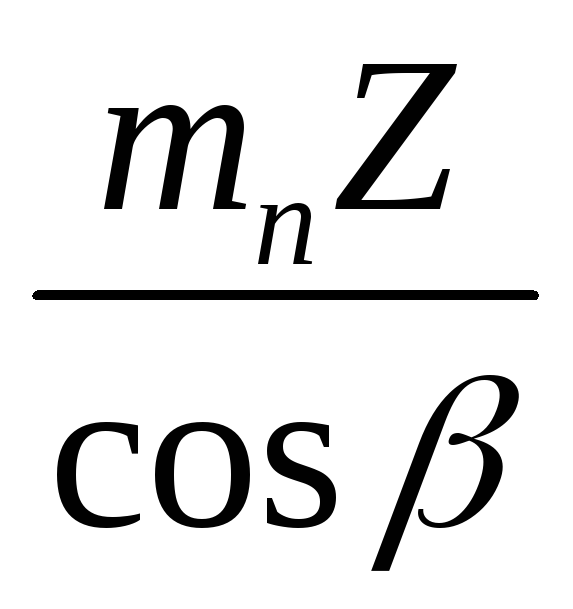
2.Ширина зубчатого венца
для шестерни b 1 = ψ ba ·a w + 5
для колеса b 2 = Ψ ba a w
3.Диаметр вершин зубьев d a = d + 2m n
4. Диаметр впадин d f = d – 2,5m n
5.Окружная
скорость V
=
Cтраница 2
Цилиндрические зубчатые передачи компактны и обладают важным свойством: они сообщают равномерное вращение ведомому колесу при равномерном вращении ведущего колеса.
Цилиндрические зубчатые передачи предназначены для передачи вращения и крутящего момента между двумя параллельно расположенными валами. Цилиндрические передачи бывают прямозубые, косозубые и шевронные с внешним, и внутренним зацеплением. К цилиндрическим относятся и реечные передачи.
Цилиндрические зубчатые передачи предназначаются для передачи равномерного вращательного движения. Для скорости получаем уравнение v dS / dta, где а - постоянная величина. Если ускорение j равно нулю, то динамические нагрузки отсутствуют. В действительности в силу неизбежных погрешностей зацепления появляются значительные динамические силы, которые нередко во много раз превышают полезную нагрузку.
Цилиндрические зубчатые передачи предназначаются для передачи равномерного вращательного движения.
Цилиндрические зубчатые передачи применяют главным образом для передачи больших мош ностей; это не исключает применение цилиндрических передач и для средни а также малых мош ностей. Конические зубчатые передачи (как и червячные передачи) применяют для средних и малых мош ностей.
Простейшая цилиндрическая зубчатая передача с внешним зацеплением показана на рис. 1.5. Механизм преобразует вращательное движение одного колеса / во вращательное движение другого колеса 2 с другой частотой вращения и моментом. Передачи с внешним зубчатым зацеплением передают вращение с изменением направления вращения.
Цилиндрические зубчатые передачи наружного зацепления могут быть изготовлены методом обкатки и методом одиночного деления на зубофрезерных, зубострогальных или зубодолбежных станках.
Цилиндрические зубчатые передачи наружного и внутреннего зацепления эвольвентного профиля бывают: прямозубые, косозубые со спиральными зубьями (геликоидальные), одинарные, блочные, шевронные, многорядные косозубые и многорядные шевронные. Конические зубчатые колеса эвольвентного профиля бывают: прямозубые, косозубые, с криволинейными зубьями, шевронные.
Дана цилиндрическая зубчатая передача: а 450 мм, степень точности 7 по всем нормам точности, вид сопряжения С.
Через цилиндрические зубчатые передачи приводится во вращение главный распределительный вал 22 (см. рис. 4.25, а), от которого вращение передается кулачкам привода механизмов поворота и переноса заготовок и выталкивателя 16 из матриц. Такое крепление обеспечивает прижим ножа к торцу отрезной матрицы по мере возрастания усилия отрезки.
Различают цилиндрические зубчатые передачи с внешним и внутренним зацеплением. Цилиндрические передачи внутреннего зацепления могут быть прямозубыми и косозубыми. Их широко применяют в самолетах, трансмиссиях легковых автомобилей, сложных планетарных механизмах, в основном там, где межосевые расстояния невелики.
Для цилиндрических зубчатых передач установлено шесть (пять для т 1 мм) классов отклонений межосевого расстояния, обозначаемых в порядке убывания точности цифрами от I (И) до VI.
Лекция 14.
Цилиндрические зубчатые передачи.
Передача непрерывного прошения от одного вала к другому с заданным передаточным отношением чаще всего осуществляется с помощью зубчатых механизмов. Зубчатые механизмы получили очень широкое применение как в машиностроении, так и в приборостроении благодаря большой надежности и точности в воспроизведения заданного закона движения. Если оси вращения валов параллельны, то применяется цилиндрическая зубчатая передача, аксоидами колес которой являются цилиндры. Такая передача относится к категории плоских механизмов. В лекциях 14-16 излагаются основы синтеза цилиндрической зубчатой передачи по заданному передаточному отношению. Эти основы называются геометрическим расчетом зубчатой передачи.
Элементы зубчатого колеса.
Цилиндрические зубчатые передачи, как отмечалось ранее, могут быть внешнего и внутреннего зацеплений. Следует также указать реечное зацепление, разграничительное между внешним и внутренним зацеплениями. Простая зубчатая передача имеет два подвижных звена, которыми являются зубчатые колеса. Рассмотрим элементы зубчатого колеса (рис. 14. l ).
Поверхность (1), отделяющая зубья от тела зубчатого колеса, называется поверхностью впадин зубьев. Поверхность (2), ограничивающая зубья со стороны, противоположной телу зубчатого колеса, - поверхность вершин зубьев. Пространство между двумя соседними зубьями (3) - впадина. Поверхность, ограничивающая зуб со стороны впадины (4), называется боковой поверхностью зуба .
Боковая поверхность состоит из главной (5) и переходной (6) поверхностей. Главная поверхность - это та часть боковой поверхности зуба, которая, взаимодействуя с главной поверхностью другого зуба, обеспечивает заданное передаточное отношение. Переходная поверхность соединяет главную поверхность с поверхностью впадин.
Главной поверхностью чаще всего является эвольвентная поверхность. так как среди цилиндрических передач особое распространение получили эвольвентные цилиндрические передачи. Объясняется это тем, что они имеют весьма значительные преимущества перед другими передачами. Так, эвольвентные передачи допускают, в определенных пределах, изменение межосевого расстояния, сохраняя при этом постоянство передаточного отношения, чего другие передачи не допускают, и обладают хорошими эксплуатационными качествами. Изготовление эвольвентных колес и инструмента для их нарезания является наиболее простым, что имеет очень важное практическое значение.
Рассмотрим образование эвольвентных поверхностей, которые будут являться главными поверхностями прямого и косого зубьев. На рис. 14.2, а в перспективе показана главная поверхность прямого зуба, которую можно представить как совокупность совершенно одинаковых эвольвент (Э, Э"), расположенных в плоскостях, перпендикулярных оси колеса. Эти эвольвенты являются траекториями точек образующей прямой КК" , принадлежащей плоскости N , которая перекатывается по основному цилиндру 1 без скольжения. Начальные точки всех эвольвент распола-гаются на образующей K b K b основного ци-линдра. Пересечение главной поверхности прямого зуба с любым соосным цилиндром 2 происходит по образующей этого цилиндра (например, прямая КК" ). Эта прямая параллельна оси колеса и называется линией прямого зуба. Главная поверхность прямого зуба является эвольвентной линейчатой цилиндрической поверхностью.
Главная поверхность косого зуба (рис. 14.2, б) также может быть представлена как совокупность одинаковых эвольвент (Э, Э"), расположенных в плоскостях, перпендикулярных оси колеса; однако в этом случае образующая прямая КК" расположена на плоскости N под некоторым углом к оси колеса. Благодаря этому при перекатывании плоскости N по основному цилиндру 1 без скольжения начальные точки эвольвент располагаются по винтовой линии K b K b на основном цилиндре. В пересечении с любым соосным цилиндром 2 главная поверхность косого зуба образует винтовую линию КК* , называемую линией косого зуба. Главная поверхность косого зуба является эвольвентной линейчатой винтовой поверхностью.
Таким образом, основное сходство главных поверхностей прямого и косого зубьев состоит в том, что в любом торцовом сечении, т. е. в сечении плоскостью, перпендикулярной оси колеса, они имеют эвольвенту.
На рис. 14.3, а изображено зубчатое колесо с внешними зубьями. Наибольший радиус r a имеет окружность вершин. На рис. 14,3. б изображено зубчатое колесо с внутренними зубьями. В этом случае тело колеса имеет форму кольца, внутрь полости которого зубья обращены своими вершинами. Поэтому радиус r a окружности вершин внутренних зубьев меньше радиуса r f окружности впадин, который является, таким образом, наибольшим. На рис. 14.3 изображены также эвольвентный профиль зуба, основная окружность, на базе которой он построен (радиус r b ), а также делительная окружность радиуса г и окружность произвольного радиуса r y .
На рис. 14.З буквой обозначен KON , равный углу профиля зуба в точке K , находящейся на делительной окружности прямозубого колеса. Этот угол стандартизован и равен 20°. Таким образом, делительная окружность прямозубого колеса является той окружностью, которая пересекает профиль зуба в точке, для которой угол профиля равен стандартному углу = 20 ° .
Если длину окружностей - делительной, основной и произвольного радиуса - поделить на число зубьев z , то получим расстояния между профилями двух соседних зубьев, называемые шагом, т. е. получим шаг по делительной окружности р , шаг по основной окружности p b и шаг по окружности произвольного радиуса p y . Дуги р , p b и p y соответствуют одному и тому же угловому шагу = p / r = p b / r b = p y / r y . Отсюда следует, что шаги пропорциональны радиусам соответствующих окружностей. Угловой шаг можно выразить и так: = 360°/ z .
Важным элементом колеса является шаг по делительной окружности. Выразим длину делительной окружности через шаг р и число зубьев колеса z : 2 r = pz . Отсюда диаметр делительной окружности d = (p /)* z = mz . Отношение p / обозначают буквой m и называют модулем зубьев колеса (единица модуля - мм). Модуль стандартизован, причем стандарт предусматривает целый ряд значений модуля. Через модуль выражают радиус делительной окружности и все линейные размеры как колеса, так и передачи:
r = m * z /2 ; (14.1)
p = * m . (14.2)
Радиус основной окружности находится из KON (рис. 14.3, а):
(14.3)
Радиус произвольной окружности колеса выражается следующим образом:
(14.4)
Так как шаги пропорциональны радиусам, то шаг по основной окружности:
а шаг по окружности произвольного радиуса:
(14.5)
Основными параметрами колес являются модуль m и число зубьев z . Размеры делительных окружностей характеризуют размеры колес и передачи. Поскольку модуль определяется из прочностного расчета, а число зубьев назначает конструктор, то для уменьшения габаритов зубчатой передачи надо уменьшать числа зубьев ее колес [см. уравнение (14.1]
Для колес с внутренними зубьями радиусы основной и делительной окружностей и шаги по этим окружностям определяют но тем же формулам, что и для колеса с внешними зубьями.
Шаг зубьев колеса по любой окружности можно представить как сумму толщины зуба s y и ширины впадины e y , т. е.
Колеса одного и того же модуля, имеющие одно и то же число зубьев, могут отличаться друг от друга толщиной зуба по делительной окружности.
Различают:
- колеса с равноделенным шагом, у которых по делительной окружности толщина зуба равна ширине впадины и, следовательно, половине шага
s = e = m/2 ;
2) колеса, у которых s > е , т. е. s > m /2 ;
3) колеса, у которых s < е , т. е. s < m /2 .
На рис. 14.3, в изображены центральные углы 2 и 2 у , соответствующие дуговым толщинам зуба s и s у , а также эвольвентные углы inv и inv y . Из рисунка следует:
b = + inv = y + inv y
отсюда
y = + inv - inv y
Выражая угловые толщины через линейные y = s y /(2 r y ) и = s /(2 r ) и подставляя из значения в уравнение, ранее составленное для y , получим формулу для определения толщины внешнего зуба:
s y = r y (s/r + 2inv - 2 inv y ) (14.6)
Аналогично составляется формула для определения толщины s y внутреннего зуба:
s y = r y (s/r - 2inv + 2 inv y )
Если безгранично увеличивать число зубьев колеса, а следовательно, и радиусы всех окружностей, то в пределе при z = все окружности преобразуются в параллельные прямые, а эвольвентный профиль зуба станет прямолинейным , что имеет очень важное практическое значение. При z = получим зубчатую рейку (рис. 14.4). В любом месте прямолинейной части зуба рейки профильный угол будет одним и тем же, равным.
Прямая UU , по которой толщина зуба рейки в точности равна ширине впадины, т. е. равна половине шага, называется делительной прямой. Шаг зубьев рейки, измеренный по любой прямой, параллельной делительной, имеет одинаковое значение p = m . Шаг рейки, замеренный по нормали n - n к ее профилю, равен mcos , т.е. равен шагу р b по основной окружности колеса, модуль которого такой же, как и модуль рейки.
Основные положения станочного зацепления.
Реечное станочное зацепление.
Способы изготовления зубчатых колес. В настоящее время зубчатые колеса изготавливают способами копирования и огибания.
По первому способу изготовляют зубчатые колеса в основном только с равноделенным шагом. При этом большинство их выполняется с заведомой погрешностью. Второй способ - способ огибания такими существенными недостатками не обладает: этим способом можно изготовить самые разнообразные зубчатые колеса и притом теоретически точно. Поэтому способ огибания нашел распространение и представляет особый интерес.
При способе огибания заготовке, из которой изготовляют зубчатое колесо, и режущему инструменту, имеющему зубчатую форму (червячная фреза, гребенка, долбяк), сообщают на станке такие движения относительно друг друга, которые воспроизводят процесс зацепления . Это зацепление называют станочным.
Помимо движений, воспроизводящих процесс зацепления инструменту сообщается еще технологическое движение резания. При этом режущие кромки инструмента описывают поверхность, называемую производящей. Укажем, что производящая поверхность и изготавливаемая боковая поверхность зуба являются взаимоогибаемыми, откуда сам способ и получил свое наименование.
При расчете геометрических параметров элементов высшей кинематической пары учитывают технологические возможности изготовления деталей на формообразующих станках (металлорежущих, прокатных станах, прессах и т. д.). Геометрия соответствующего формообразующего инструмента тесным образом связана с производящими поверхностями . Для инструментов, осуществляющих процесс формообразования путем срезания стружки, такой производящей поверхностью является воображаемая поверхность, содержащая режущие кромки инструмента или образуемая при их главном движении, необходимом для резания. Если режущие кромки - прямые, а главное движение - прямолинейное, то производящей поверхностью является плоскость. Если режущие кромки криволинейные, а главное движение - прямолинейное, то производящей поверхностью является цилиндрическая поверхность (например, эвольвентная поверхность для долбяков).
Зацепление проектируемой поверхности зубьев с производящей поверхностью по аналогии с зацеплением нарезаемого колеса с производящей поверхностью режущего инструмента называют станочным зацеплением . Этот термин был предложен В. А. Гавриленко, крупным ученым, обобщившим и развившим основные положения теории зацепления эвольвентных передач. Сущность станочного зацепления заключается в том, что производящая поверхность (поверхность режущих кромок инструмента) и проектируемая поверхность зуба («нарезаемого» колеса) имеют такое же относительное движение, какое имели бы зубчатые колеса при зацеплении друг с другом при взаимодействии аксоидных поверхностей.
При нарезании цилиндрических зубчатых колес оси производящего колеса (т. е. воображаемого зубчатого колеса, у которого боковые поверхности являются производящими поверхностями) и проектируемого («нарезаемого») колеса параллельны между собой и аксоидами являются цилиндры. Если производящее колесо имеет конечное число зубьев, то режущими инструментами являются долбяк (рис. 14.5 е), абразивный хон (рис, 14.5 ж), которыми можно обрабатывать боковые поверхности зубьев колес с различными числами зубьев (рис, 14.5, з). При бесконечно большом радиусе аксоида производящего колеса инструмент должен иметь бесконечно большое число зубьев, т. е. превратиться в рейку. В этом случае инструментом обычно являются червячная фреза (рис. 14.5, б) или абразивный червячный круг (рис. 14.5, г), у которых реечный производящий контур (рис. 14.5, д) расположен на винтовой поверхности. Частным случаем является инструмент, называемый зуборезной гребенкой (рис. 14.5, а) или пара тарельчатых шлифовальных кругов (рис. 14.5, в). Главным движением резания у долбяка, гребенки и абразивного хона является поступательное движение, а у червячной фрезы и
шлифовальных кругов - вращательное движение.
В процессе движения огибания (обкатки) основной шаг инструмента по профильной нормали соответствует основному шагу проектируемого («нарезаемого») колеса. Процесс перехода от формообразования одного зуба к другому в процессе обкатки осуществляется автоматически при непрерывном относительном движении (рис. 14.5, д. з).
Если производящую поверхность рассечь плоскостью, перпендикулярной оси нарезаемого колеса, то в сечении получим исходный производящий контур (ИПК). Станочное зацепление есть зацепление ИПК с профилем зуба нарезаемого колеса.
Рассмотрим реечное станочное зацепление, т. е. такое, когда ИПК имеет очертания зубчатой рейки. Эвольвентные кромки этого ИПК прямолинейны. Режущий инструмент (червячная фреза или гребенка), образующий своим главным движением эвольвентный реечный ИПК, обладает очень ценным свойством: его можно изготовить, сравнительно дешево и точно. Геометрия зубьев нарезаемого колеса определяется параметрами ИПК реечного инструмента и его расположением по отношению к колесу.
Исходный производящий контур эвольвентного реечного инструмента . Форма я размеры ИПК стандартизованы. Эвольвентные части профиля зубьев ИПК (рис. 14.6, а) прямолинейны и наклонены к оси зуба под углом. Переходы от прямолинейной части зуба к основанию впадины и к вершине осуществлены по дуге радиусом t . Точки сопряжения отмечены на ИПК буквами А, С, D , Е . Прямолинейная часть CD является эвольвентной, а скругления АС и DE - неэвольвентной частью контура. Прямая, разделяющая зуб по высоте на две равные части, называется делительной. На ИПК отмечаются еще четыре линии, параллельные делительной прямой и проходящие по основаниям впадин зубьев, по их вершинам и через точки сопряжения С и О . Расстояния между этими прямыми выражают размеры зуба исходного производящего контура по высоте и измеряются соответственно величинами h a = h a * m и C = c * m , где h a * - коэффициент высоты зуба, с * - коэффициент радиального зазора. Согласно стандарту: h a * = 1,0 ; с * = 0,25 . Прямые, проходящие через точки С и D , называются прямыми граничных точек.
Размерами вдоль делительной прямой являются шаг, толщина зуба н ширина впадины. Шаг р исходного производящего контура, измеренный по любой прямой, параллельной делительной, есть величина постоянная, равная m , где m - стандартный модуль. Толщина зуба ИПК по делительной прямом равна ширине впадины s 0 = e 0 = m /2 , а вместе они составляют шаг. Угол профиля зуба стандартизован: = 20° . Радиус скругления (дуги DE )
(14.7)
Таким образом. ИПК реечного инструмента характеризуется четырьмя стандартными параметрами: m , h a * , c * .
Реечное станочное зацепление и коэффициент смещения . Реечное станочное зацепление, как и всякое зацепление, имеет начальные линии. Ими являются станочно-начальная прямая рейки и станочно-начальная окружность колеса, которые катятся друг по другу без скольжения. Можно показать, что в реечном станочном зацеплении радиус r w 0 станочно-начальной окружности равен радиусу делительной окружности r .
Угол реечного станочного зацепления w 0 равен профильному углу а исходного производящего контура (как углы с взаимно перпендикулярными сторонами). Отметим также, что угол профиля зуба колеса в точке, находящейся на делительной окружности, равен профильному углу исходного производящего контура.
На станке инструмент можно расположить по-разному относительно нарезаемого колеса. Поэтому в станочном зацеплении делительная прямая ИПК может располагаться различным образом по отношению к делительной окружности колеса: I) она может касаться делительной окружности - нулевая установка инструмента; 2) быть отодвинутой от нее положительная установка; 3) пересекать ееотрицательная установка.
Расстояние между делительной прямой и делительной окружностью называется смещением инструмента . Его выражают в виде произведения модуля m на коэффициент смещения х и ему присваивают знак. При нулевой установке смещение m х > 0, х > 0 . При положительной установке m х > 0, х > 0. При отрицательной установке смещением является стрелка сегмента, которую делительная прямая отсекает от делительной окружности; в этом случае mx < 0, x < 0.
На рис. 14.6, а изображено реечное станочное зацепление при нарезании зубчатого колеса с положительным смещением и указаны все элементы производящего исходного контура, нарезаемого колеса и станочного зацепления.
Линия реечного станочного зацепления начинается в точке N и через полюс P 0 уходит в бесконечность. Длина ее активной части ограничена точками В 1 и B , находящимися на пересечении линии станочного зацепления с прямой QQ граничных точек и окружностью вершин (рис. 14.6, а)
Профиль зуба колеса имеет эвольвентную и неэвольвентную части. Переход эвольвснтного профиля в неэпольвентиый находится на окружности граничных точек колеса, радиус которой r l = OB 1 " .
Расстояние между окружностью вершин зубьев колеса и прямой впадин ИПК представляет собой станочный зазор С 0 . Величина его складывается из двух частей: с * m , ym , где у коэффициент уравнительного смещения.
Размеры изготовляемого зубчатого колеса с внешними зубьями . Диаметр вершин прямозубого колеса (рис. 14.6, а):
(14.8)
Высота зуба из того же рисунка:
(14.9)
Если x = 0 (смещения инструмента нет) и у = 0 , то d a = m (z + 2 h a * ) , h = m (2 h a * + с * ) , и при стандартных значениях h a * = 1,0 и с * = 0,25 получим d a = m(z +2) и h = 2,25 m .
Стачочно-начальная прямая перекатывается по станочно-начальной окружности (она же делительная) без скольжения. Поэтому толщина зуба s по делительной окружности нарезаемого колеса равна ширине ММ впадины по станочно-начальной прямой ИПК (рис. 14.6, б ).
Отрезок ММ складывается из ширины впадины ИПК по делительной прямой e 0 = m /2 и двух катетов, каждый из которых равен xm tg , поэтому:
s = m/2 + 2 xm tg (14.10)
Если инструмент установлен относительно колеса без смещения ( xm = 0), то s = m /2 ; значит, толщина зуба s по делительной окружности колеса равна ширине впадины е , так как s + е = m . В этом случае получается колесо с равноделенным шагом s = e , Если xm > 0 , то s > m /2 и, следовательно, s > e . Если xm < 0, то s < m /2 , и поэтому s < e .
При нарезании косозубых колес применяется тот же инструмент 1 , что для прямозубых, но устанавливается он наклонно под углом по отношению к торцовой плоскости t - t колеса (заготовки) (рис. 14.6, в ). На этом рисунке показана развертка 2 делительного цилиндра косозубого колеса, в результате чего винтовые линии косого зуба преобразовались в прямые линии. В торцовой плоскости t - t косозубого колеса вследствие наклона инструмента шаг увеличивается и становится равным p / cos , а следовательно, и модуль в торцовой плоскости будет нестандартным, равным m / cos . Поэтому при расчете линейных размеров косозубого колеса по формулам, в которые входит стандартный модуль, вместо m следует подставлять m / cos , например делительный диаметр косозубого колеса d = zm / cos .
Обратим внимание на размеры h a * m , c * m , xm , y * m , перпендикулярные делительной прямой (рис. 14.6, а ), которые принято называть размерами по высоте. На рис. 14.6 в эти размеры расположены перпендикулярно плоскости рисунка. Поэтому при повороте инструмента на угол размеры по высоте не изменяются. А отсюда следует, что когда в уравнениях встречаются произведения h a m , cm , xm , ym , то их при расчете косозубой передачи можно подставлять в эти уравнения без всякого пересчета сомножителей. Так, например, формула диаметра вершин косозубого колеса может быть записана следующим образом: d a = d + 2(h a * m + xm - y * m ) .
Угол профиля исходного производящего контура при нарезании косозубого колеса увеличивается по сравнению со стандартной величиной = 20°, поскольку размеры по высоте не изменяются, а шаг в торцовом сечении увеличивается. Расчетный угол профиля t исходного производящего контура при нарезании косозубых колес определяют по формуле:
На рис. 14.7 сравниваются профили зубьев трех колес, имеющих одинаковые числа зубьев, нарезанные одним и тем же инструментом, но с различными смещениями: x 1 < x 2 < x 3 . Колеса имеют одинаковые радиусы делительных и основных окружностей; следовательно, профили зубьев всех трех колес очерчены по одной и той же эвольвенте. Но толщины зубьев s 1 , (дуга ab ), s 2 (дуга ас ), s 3 (дуга af ) и радиусы окружностей вершин r a 1 , r a 2 , r a 3 , у колес будут разные. По мере увеличения х толщина зуба у основания увеличивается, а у вершины уменьшается, т. е. коэффициент смещения существенно влияет на форму зуба. Следовательно, назначая при проектировании тот или иной коэффициент смещения, можно влиять на форму зубьев колёс и на качество зубчатой передачи, наделяя её желательными свойствами.
Контрольные вопросы к лекции
N
14
- Что называют зубчатым колесом?
- Расскажите об основных элементах зубчатого колеса.
- Запишите формулы окружного и углового шагов эвольвентного зубчатого колеса.
- Какие методы изготовления зубчатых колёс Вы знаете?
- В чём заключается сущность изготовления эвольвентных колёс методом огибания?
- Дайте определение станочного зацепления.
- Выведите формулы для определения основных размеров зубчатого колеса () используя схему станочного зацепления.