Учитывая условия и характер работы открытых передач (недостаточная защищённость от загрязнения абразивными частицами и увеличенный абразивный износ при плохой смазке, большие деформации валов, что приводит к увеличению зазоров в зацеплении, возрастанию динамических нагрузок, к понижению прочности изношенных зубьев вследствие уменьшения площади их поперечного сечения и, как следствие, к поломке зубьев), данные передачи рекомендуют рассчитывать по напряжениям изгиба. В этих передачах выкрашивание не наблюдается, так как поверхностные слои зубьев изнашиваются и удаляются раньше, чем появляются усталостные трещины.
Для проектного расчёта открытых передач по напряжениям изгиба определяют модуль зацепления из выражений:
− для прямозубых колес
− для косозубых колес
Здесь: z 3 − число зубьев шестерни открытой передачи (см. исходные данные);
−коэффициент ширины зубчатого венца колеса относительно начального диаметра шестерни, рекомендуют назначать для открытых передач = 0,1…2,0;
−допускаемое напряжение изгиба зубьев шестерни, Н/мм 2 , определяют в соответствии с п. 2.3. («Расчет допускаемых напряжений»);
Т 3 − момент на шестерне, Нм; ;
−смотри выше, для проектного расчета принять = 0,8;
−смотри рис. 2.3;
Y F 3 − смотри табл. 2.9.
Полученное значение модуля округляют в большую сторону до значения из стандартного ряда модулей (см. п. 2.5).
Зная значение модуля, определяют геометрические размеры шестерни:
диаметр делительный − или
диаметр вершин
зубьев −
диаметр впадин
зубьев −
ширина венца −
Точность вычисления диаметров шестерни до 0,001 мм, значение ширины зубчатого венца округляют до целого числа по нормальным линейным размерам (см. табл. 2.5). Проверочный расчет такой передачи по контактным напряжениям выполняют в соответствии с п. 2.6. («Проверочный расчет закрытой цилиндрической передачи»).
2.8. Расчёт закрытой конической зубчатой передачи
Наибольшее применение в редукторостроении получили прямозубые конические колёса, у которых оси валов пересекаются под углом (рис. 2.4), так называемые ортогональные передачи.
Рис. 2.4
Проектный расчёт
Основной габаритный размер передачи − делительный диаметр колеса по внешнему торцу − рассчитывают по формуле:
,
где Е
МПа;
T 2 − вращающий момент на валу колеса, Нмм (см.п.2.4);
−коэффициент неравномерности распределения нагрузки по длине зуба, определяют по графикам на рис. 2.5.
Здесь К be − коэффициент ширины зубчатого венца относительно внешнего конусного расстояния, К be = b w / R e . Рекомендуют принять . Меньшие значения назначают для неприрабатываемых зубчатых колёс, когдаH 1 и H 2 > 350 HB или V > 15 м/с.
Рис. 2.5
Наиболее распространено в редукторостроении значение К be = 0,285, тогда предыдущее выражение для определения делительного диаметра по внешнему торцу колеса принимает вид
,
где u p – расчетное передаточное число конической передачи, илиu p = z 2 / z 1 .
Геометрический расчёт
Определяют делительный диаметр шестерни по внешнему торцу .
По значению определяют число зубьев шестерни:
При Н 1 и ,
При Н 1 и .
Вычисленное значение z 1 округляют до целого числа.
Рис. 2.6
Определяют число зубьев колеса .
Вычисленное значение округляют до целого числа. После этого необходимо уточнить:
Передаточное число передачи ,
Угол делительного конуса колеса ,
Угол делительного конуса шестерни ,
Внешний окружной
модуль .
Рекомендуется
округлить m
e
до стандартного значения m
e
ф
по ряду модулей: 1,5; 2; 2,5; 3; 4; 5; 6; 8; 10. После
этого уточняют величины диаметров
и
.
Рассчитывают величину внешнего конусного расстояния передачи (рис. 2.4) .
Рабочая ширина зубчатого венца колеса определяют как .
Полученное значение округляют до ближайшего из ряда нормальных линейных размеров (табл. 2.5).
Определяют расчётный модуль зацепления в среднем сечении зуба
При этом найденное значение m m не округляют!
Рассчитывают внешнюю высоту головки зуба .
Внешнюю высоту ножки зуба определяют как .
Внешний диаметр вершин зубьев колёс рассчитывают по формуле .
Угол ножки зуба
рассчитывают по формуле
.
Проверочный расчёт
При расчёте на выносливость зубьев колёс по контактным напряжениям проверяют выполнение условия
,
где E
пр
− приведённый модуль упругости, для
стальных колёс
МПа;
−вращающий момент на шестерне, Нмм, ;
Введение……………..…………………………………..……………..2
1. Анализ кинематической схемы…………..……..………………..2
2. Кинематический расчет привода…………………………………3
3. Определение геометрических параметров цилиндрической
зубчатой передачи………………………………………….…………..6
4. Геометрический расчет конической зубчатой передачи………9
5. Определение геометрических размеров и расчет на
прочность выходного вала…………………………………………….11
6. Проверочный расчет подшипника..……………………………….16
7. Список использованной литературы……………………………..18
Редуктор - это механизм состоящий из зубчатых или червячных
передач, заключенный в отдельный закрытый корпус. Редуктор
предназначен для понижения числа оборотов и, соответственно, повышения крутящего момента.
Редукторы делятся по следующим признакам:
По типу передачи - на зубчатые, червячные или зубчато-червячные:
По числу ступеней - на одноступенчатые (когда передаче осуществляется одной парой колес), двух-, трех- или многоступенчатые:
По типу зубчатых колес - на цилиндрические, конические,иликоническо-цилиндрические;
По расположению валов редуктора в пространстве - на горизонтальные, вертикальные, наклонные:
По особенностям кинематической схемы " на развернутую, соосную. с раздвоенной ступенью.
1. Анализ кинематической схемы
Наш механизм состоит из привода электромашинной (1),муфты (2), цилиндрической шестерни (3), цилиндрические колеса (4), конической шестерни (5), конического колеса (6), валов (7,6,9) и трех пар подшипников качения. Мощность на ведомом валу N 3 =9,2 кВт, угловая скорость п 3 = 155 об/мин, привод предназначен для длительной работы, допускаемое отклонение скорости
5%,
2. Кинематический расчет привода
2.1. Определяем общий КПД привода
h=h 1 *h 2 *h 3 3 *h 4Согласно таблице 5 (1) имеем
h 1 =0,93 - КПД прямозубой цилиндрической передачи;
h 2 =0,9 - КПД конической передачи;
h 3 =0,98 - КПД подшипников качения;
h 4 =0,98 - КПД муфты
h = 0,93 * 0,98 3 * 0,9 * 0,98 = 0,77
2.2. Определяем номинальную мощность двигателя
N дв =N 3 /h=11,9 кВт
2.3. Выбираем тип двигателя по таблице 13 (2). Это двигатель
А62 с ближайшим большим значением мощности 14 кВт. Этому значению номинальной мощности соответствует частота вращения 1500 об/мин.
2.4. Определяем передаточное число привода
i = i ном /n 3 = 1500/155 = 9,78
2.5. Так как наш механизм состоит из закрытой цилиндрической передачи и открытой конической передачи, то разбиваем передаточноечисло на две составляющих:
2.6. Уточняем общее передаточное число
i = g.5 * 4 = 10
2.7. Определяем максимально допустимое отклонение частоты вращения выходного вала
- допускаемое отклонение скорости по заданию.2.8. Допускаемая частота вращения выходного вала с учетом отклонений
2.9. Зная частные передаточные отношения определяем частоту вращения каждого вала:
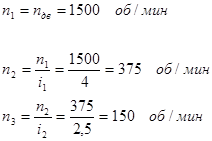
Таким образом, частота вращения выходного вала находитсяв пределах допустимой.
2.10. Определяем крутящие моменты, передаваемые валами механизма с учетом передаточных отношений и КПД:

![]() |
2.11 Аналогично определяем мощность, передаваемую валами
2.12. Построим график распределения крутящего момента и мощности по валам привода
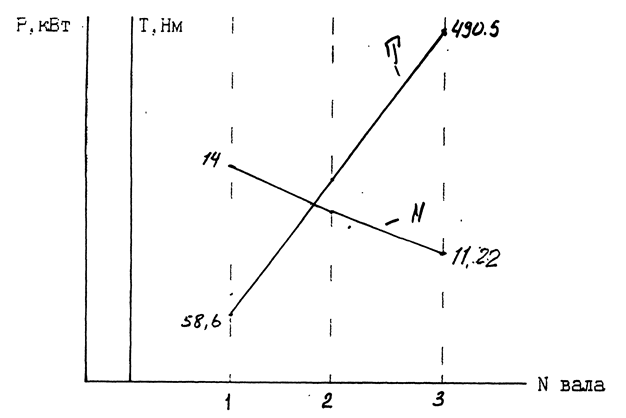
3. Определение геометрических параметров цилиндрической зубчатой передачи
3.1. Для колес со стандартным исходным контуром, нарезаемым без смещения режущего инструмента (х = 0), число зубьев шестерни рекомендуется выбирать в пределах от 22 до 26. Выбираем Z 1 = 22
3.2. Число зубьев колеса:
Z 2 = Z 1 * i 1 = 22 * 4 = 88
3.3. Определяем межосевое расстояние по формуле

где K a - вспомогательный коэффициент, для косозубых передач равен 43;
- коэффициент ширины венца шестерни расположенной симметрично относительно опор, по таблице 9(3) равен 0,4; - передаточное число;T 2 - вращающий момент на тихоходном валу;
По таблице 3.1 (3) определяем марку стали для шестерни - 40Х. твердость > 45HRC: для колеса - 40Х. твердость
350НВ.По таблице 3.2 (3) для шестерни


Полученное значение межосевого расстояния для нестандартных передач округляем до ближайшего из ряда нормальных линейных размеров, A W = 100 мм.
3.4. Определяем модуль зацепления по формуле
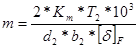
где К m , - вспомогательный коэффициент, длякосозубых передач равен 5,8;


Полученное значение модуля округляем в большую сторону до стандартного из ряда стр.59 (3). Для силовых зубчатых передач при твердости одного из колес > 45HRC. принимается модуль > 1.5. поэтому принимаем модуль m=2.
3.5. Определяем угол наклона зубьев для косозубых передач:
3.6. Определяем суммарное число зубьев шестерни и колеса для косозубых колес
Полученное значение округляем в меньшую сторону до целого числа, то есть Z = 100.
3.7. Определяем число зубьев шестерни

3.8. Определяем число зубьев колеса
Z 2 = Z - Z 1 = 100 - 20 == 80
3.9.Определяем фактическое передаточное число и проверяем его отклонение

следовательно передаточное число выбрано верно.
3.10. Определяем основные геометрические параметры передачи и сводим их в таблицу
Параметры | Формулы | Колесо | |
1 | Число зубьев | Z 2 | 80 |
2 | Модуль нормальный, мм | m n =m | 2 |
3 | Шаг нормальный, мм | 6,28 | |
4 | Угол исходного контура | ||
5 | Угол наклона зубьев | ||
6 | Торцовый модуль, мм | 2,03 | |
7 | Торцовый шаг, мм | 2,03 | |
8 | Коэффициент головки зуба | H | 1 |
9 | Коэффициент ножки зуба | С rn > 1 | 0.25 |
10 | Диаметр делительной окружности, мм | d = Z * m t | 162.4 |
11 | Высота делительной головки зуба, мм | h a = h * m | 2 |
12 | Высота делительной ножки зуба, мм | H f = (h + C)*m | 2,5 |
13 | Высота зуба, мм | h = h a + h f | 4.5 |
l4 | Диаметр окружности выступов, мм |
d a = d + 2 h a | 166.4 |
15 | Диаметр окружности впадин, мм | d f =d - 2h f | 155,4 |
16 | Межосевое расстояние, мм | A = 0,5 (d 1 + d 2) | 100 |
17 | Ширина венца, мм | 40 |
4. Геометрический расчет конической зубчатой передачи
4.1 Определяем делительный диаметр колеса

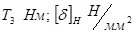
V Н - коэффициент вида конических колес, для прямозубых равен 1.

Полученное значение внешнего делительного диаметра колеса округляем до ближайшего значения из ряда нормальных линейных размеров табл.13.15 (3).
d е4 =250 мм
4.2. Определяем углы делительных конусов шестерни и колеса
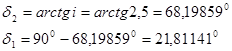
4.3. Определяем внешнее конусное расстояние
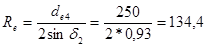
4.4. Определяем ширину зубчатого венца

4.5. Определяем внешний окружной модуль

где К f b - коэффициент, учитывающий распределение нагрузки по ширине венца, равен 1; (3)
V f = 0,85 - коэффициент вида конических колес. (3)

Так как передача открытая, увеличиваем значение модуля на 30%, то есть m = 5 мм.
4.6. Определяем число зубьев колеса и шестерни

4.7. Определяем фактическое передаточное число.

4.8. Определяем внешние диаметры шестерни и колеса:
делительный
;вершин зубьев
=109,28 мм; = 253,71 мм;впадин зубьев


средний делительный диаметр
=85,7 мм;
5. Определение геометрических размеров и расчет на прочность выходного вала
5.1. Определяем силы действующие в зацеплении конической прямозубой передачи:
окружная

радиальная
= 612 Н, = 1530 Н.5.2 Выбираем материал для вала по таблице 3.2 (3). Это сталь 45 улучшенная, со следующими механическими характеристиками:
допускаемое напряжение на кручение
5.3. Ориентировочно определяем геометрические размеры каждой ступени вала:
Диаметр выходной части
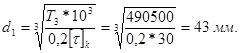
Принимаем d 1 = 45 мм.
Исходя из этого принимаем диаметр под подшипником d 2 = 50 мм.
5.4. Выбираем предварительно подшипники качения. По таблице 7.2 (3)для конической передачи при n<1500 об/мин применяется подшипник роликовый конический однорядный. Выбираем типоразмер подшипника по величине диаметра внутреннего кольца, равного диаметру d 2 = 50мм. Это подшипник легкой широкой серии 7510: d = 50мм, D = 90мм, Т = 25 мм, угол контакта 16 0 , C r =62 kH.
5.5. Вычерчиваем ступени вала по размерам, полученным вориентировочном расчете и определяем расстояния между точками приложения реакций подшипников.
5.6. Вычерчиваем схему сил в зацеплении конической передачи.
5.7. Определяем реакции опор:
а) вертикальная плоскость

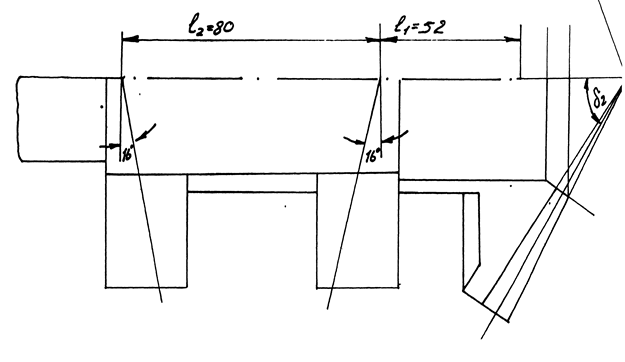
б) строим эпюру изгибающих моментов в характерных сечениях A, B, C(рис. 5.1)
в) горизонтальная плоскость,


ОЦЕНКА РАБОТОСПОСОБНОСТИ ЗУБЧАТЫХ ЦИЛИНДРИЧЕСКИХ ПЕРЕДАЧ
П л а н л е к ц и и
1. Условия работоспособности.
2. Расчетные удельные нагрузки.
3. Алгоритм проектирования зубчатой передачи.
4. Расчеты зубчатых передач на контактную прочность. Программа
5. Определение напряжений при изгибе зубьев. Программа ZUCF.
6. Особенности расчетов косозубых и шевронных цилиндрических передач.
1. Условия работоспособности
Передача нагрузки в зубчатой передаче происходит в результате соприкосновения боковых профилей сопряженных зубьев. Под действием сил давления зубья находятся в сложнонапряженном состоянии. При этом нагружается и поверхность зубьев (линейный контакт), и весь объем зуба. Поэтому работоспособность передачи оценивается контактной прочностью боковой поверхности зубьев и объемной прочностью зуба при сложном нагружении. Оценка прочности зубьев усложняется действием переменной нагрузки на зуб, изменяющейся по прерывистому пульсирующему циклу.
При недостаточной контактной прочности поверхности зубьев происходит усталостное выкрашивание рабочих поверхностей.
Поломки зубьев в основном тоже носят усталостный характер и происходят либо при перегрузках передачи, либо при недостаточной их объемной прочности. При объемном нагружении зубьев главным видом деформации является изгиб. Поэтому оценку объемной прочности зубьев обычно проводят по деформации изгиба. Таким образом, в зубчатых передачах при оценке работоспособности используют два условия:
а) условие контактной прочности поверхности
Условия оптимизации параметров передачи. Стандартная эвольвент-
ная зубчатая передача обеспечивает неразрывность контакта зубьев в процессе работы и постоянное передаточное отношение в пределах допустимой
погрешности. Для такой передачи основной критерий работоспособности – обеспечение контактной и изгибной прочности зубьев. Поэтому основная целевая функция оптимизации для закрытых зубчатых передач будет выражена условием контактной прочности поверхности зубьев при допускаемой 20%-ной недогрузке передачи и ее 10%-ной перегрузке, т. е.
0,8 H /H 1,1,
где H – фактические контактные напряжения на поверхности зуба, Н/мм2 ;H – допускаемые контактные напряжения для материала колес.
Такая целевая функция, ввиду невозможности однозначного решения, имеет большое число вариантов.
В то же время для зубчатой передачи желательно ввести целый ряд дополнительных условий проектирования и эксплуатации: обеспечение оптимальной изгибной прочности зубьев, минимальных габаритных размеров и массы, стандартного значения модуля и межосевого расстояния, минимального отклонения передаточного отношения, минимального момента инерции передачи и др. Такие дополнительные условия позволяют ввести в расчет дополнительные ограничительные функции и тем самым сократить количество неопределяемых параметров влияния.
В рассматриваемой методике введены следующие условия ограничительных функций:
оптимальная прочность по изгибу зуба: для шестерни
0,8 F ш /F ш 0,1,
для колеса
0,8 F к /F к 1,1;
минимальное число зубьев;
минимальное отклонение передаточного отношения;
обеспечение стандартных значений модуля и межосевого расстояния;
снижение до минимума неравномерности распределения нагрузки по длине зуба за счет минимизации ширины венца;
минимальный угол наклона зубьев из условия торцевого перекрытия;
минимальная масса и момент инерции колес;
оптимальные коэффициенты смещения инструмента из условия наибольшей прочности зуба;
оптимальные твердость и марка материала из условий эксплуатации. В условия работоспособности необходимо внести ряд существенных
дополнений, учитывающих специфику нагружения, конструкции и условий эксплуатации передач.
2. Расчетные удельные нагрузки
При составлении расчетных схем для зубчатых передач схематизацию нагрузки выполняют путем введения расчетной удельной нагрузки, под которой понимают величину условной нагрузки от окружного усилия F t , приходящейся на единицу рабочей ширины зубчатого колеса. Если обозначить расчетную удельную нагрузку черезq , то ее величину можно определить из выражения
где K – коэффициент нагрузки;b w – рабочая ширина зубчатого колеса. Коэффициент нагрузки вводится с целью компенсации неучтенных
дополнительных напряжений, возникающих из-за сложного нагружения зубьев, особенностей конструкции и эксплуатации колес. Проблема выбора значения коэффициента нагрузки в зубчатых передачах – одна из сложных.
По методике расчета эвольвентных зубчатых передач, рекомендованной ГОСТ 21354–75, значения коэффициента нагрузки определяются по следующим зависимостям:
K HK Hβ K Hα K Hv, | K FK Fβ K Fα K Fv, |
где K H β ,K F β – коэффициенты концентрации нагрузки по ширине зубчатого венца соответственно при контактной выносливости и изгибе;K H α ,K F α – коэффициенты, учитывающие распределение нагрузки между зубьями соответственно при контактной выносливости и изгибе;K H ν ,K F ν – коэффициенты, учитывающие динамическую нагрузку в зацеплении соответственно при контактной выносливости и изгибе.
Для определения величин коэффициентов в справочной литературе приводятся соответствующие графики, таблицы, формулы и аппроксимирующие зависимости. Рассмотрим эти зависимости.
Коэффициент распределения нагрузки между зубьями определяют по зависимостям для косозубых колес:
K H α (0, 0026ST 0, 013)v 0, 027ST 0,84;
KF α | 4 εα | 1 ST 5 | |
4εα |
|||
где ST – степень точности передачи;v – окружная скорость зубьев; εα – коэффициент торцевого перекрытия.
Для прямозубых колес значения обоих коэффициентов принимаются равными единице.
Таблица 6.1 |
||||
Значения коэффициентов Н иF | ||||
Вид передачи | Коэффициенты | Твердость поверхности |
||
Прямозубая | ||||
Косозубая | ||||
При проектных расчетах, когда размеры колес неизвестны, окружную скорость движения приближенно можно определить по формуле
где q Hv ,q Fv – удельные окружные динамические силы, Н/мм. Значения этих сил должны удовлетворять следующим соотношениям:
qHv δ H g0 vaw i qпред ;
qFv δ F g0 vaw i qпред .
Здесь Н ,F – коэффициенты, учитывающие вид зубчатой передачи (табл. 6.1);g 0 – коэффициент, учитывающий влияние разности окружных шагов колес;
Значения коэффициентов концентрации нагрузки по ширине зубчатого венца зависят от коэффициента ширины зубчатого венца bd =b w /d w и номера схемы, по которой выполнен монтаж колес:
при твердости поверхности зубьев НВ 350
K H = 1 + 0,51bd /NS ; |
при твердости НВ > 350 | ||
K H = 1 + 1,1bd /NS ; | K F = 1 + 1,8bd /NS , |
где NS – номер схемы, учитывающий расположение колес и другие характеристики передачи относительно опор.
3. Расчеты зубчатых передач на контактную прочность.
При оценке работоспособности по условию контактной выносливости (6.1) необходимо вычислить фактические контактные напряжения, возникающие на боковых поверхностях зубьев.
Экспериментальные исследования показывают, что разрушение профилей зубьев начинается в местах, расположенных в зоне начальных окружностей. Для определения контактных напряжений можно воспользоваться формулой Герца – Беляева для вычисления максимального нормального напряжения в зоне соприкосновения двух цилиндров по линейному контакту:
где – приведенный модуль упругости; ρ – приведенный радиус кривизны поверхности; µ – коэффициент Пуассона.
Для учета специфики нагружения и условий эксплуатации зубчатых передач в формулу (6.13) необходимо ввести ряд дополнений.
Определим напряжения для зубчатой передачи в момент, когда точка контакта зубьев находится в полюсе зацепления P (рис. 6.2).
Интенсивность нагрузки q , с которой прижаты друг к другу зубья колес, найдем, если разделим полную расчетную силу давленияF n на длину контактной линииl , т. е.
q = Fn / l.
Для передачи с косыми зубьями полную расчетную силу давления зубьев определим через окружное усилие F t и коэффициент нагрузкиK H :
F tK H | |||
где α – угол профиля зуба; β – угол наклона зуба.
Учитывая, что в косозубом зацеплении длина зуба l зависит от угла его наклона β, ширины колесаb w и коэффициента перекрытия зубьев, перепишем зависимость (6.3) в следующем виде:
F tK Hcosβ | F tK H | ||||||||||||||||||||||||||||||
cos α cosβ b K | cosα b K | ||||||||||||||||||||||||||||||
где K | – коэффициент | степени перекрытия; | прямозубых передач |
||||||||||||||||||||||||||||
Для косозубых передач K = . | |||||||||||||||||||||||||||||||
Обозначим q | Тогда предыдущая зависимость примет вид |
||||||||||||||||||||||||||||||
q qt | |||||||||||||||||||||||||||||||
cos α K | |||||||||||||||||||||||||||||||
При соприкосновении зубьев в полюсе радиусы кривизны эвольвент |
|||||||||||||||||||||||||||||||
зубьев 1 =N 1 и | N 2 . | ρ1 O 1 P sin α |
|||||||||||||||||||||||||||||
Учитывая, | ∆О 1 N 1 P и ∆О 2 N 2 P (рис | ||||||||||||||||||||||||||||||
и ρ2 O 2 P sin α , | определим | приведенный | кривизны | сопряженных |
|||||||||||||||||||||||||||
поверхностей: | |||||||||||||||||||||||||||||||
ρ1 ρ2 | d w 1 sin αd w 2 sin α | ||||||||||||||||||||||||||||||
sin α |
|||||||||||||||||||||||||||||||
2cosβ |
где d w 1 иd w 2 – начальные диаметры первого и второго колеса;d w 1 =О 1 Р иd w 2 =О 2 Р ; знак плюс используется для внешнего зацепления; знак минус – для внутреннего.
После соответствующих преобразований получим
d w 1 sin αi | ||||||||||||||||||||||||
2 i 1 cosβ | ||||||||||||||||||||||||
Подставим значения q и ρ из выражений (6.15) и (6.17) в зависимость |
||||||||||||||||||||||||
(6.14) получим | ||||||||||||||||||||||||
ζH 0, 418 | q i E 2i 1 cosβ | |||||||||||||||||||||||
cos α K ε 1 μ2 | d w 1 sin αi |
|||||||||||||||||||||||
Для практических расчетов по ГОСТ 21354–75 введены следующие |
||||||||||||||||||||||||
условные обозначения: | ||||||||||||||||||||||||
– коэффициент, учитывающий механические свойства |
||||||||||||||||||||||||
материалов сопряженных зубчатых колес; | ||||||||||||||||||||||||
– коэффициент, учитывающий форму | сопряженных |
|||||||||||||||||||||||
поверхностей зубьев в полюсе зацепления; | ||||||||||||||||||||||||
Z ε1/ K ε | – коэффициент, учитывающий суммарную длину контакт- |
|||||||||||||||||||||||
ных линий. | ||||||||||||||||||||||||
С учетом этих обозначений зависимость (6.18) примет вид | ||||||||||||||||||||||||
ζ HZ м Z HZ ε | qi i1 | |||||||||||||||||||||||
dw 1 i | ||||||||||||||||||||||||
Формула (6.19) позволяет вычислить контактные напряжения для прямозубых и косозубых передач внешнего и внутреннего зацеплений.
4. Определение напряжений при изгибе зубьев
При оценке напряжений изгиба принимают, что зуб ведомого колеса испытывает наибольшие напряжения в начале зацепления, а вся нагрузка передается одной парой зубьев в течение всего периода зацепления. Экспериментальные исследования показывают, что ошибки изготовления, приводящие к расхождению окружных шагов, не компенсируются полностью деформациями зубьев. В результате наиболее нагруженными зубья будут в начале и в конце зацепления.
Расчетную схему зуба можно представить в виде жестко защемленной балки, нагруженной нормальной силой F , приложенной к вершине зуба (рис. 6.3). Возникающая сила тренияF тр между зубьями приводит к отклоне-
нию силы нормального давления на угол трения. Величину силы F" находят по формуле
F" =F /cos . |
Пользуясь приемами схематизации, проведем координатные оси xOz , переместив начало координат из точки пересечения линии действия силыF
в точку О на ось симметрии зуба, а осьх направив вдоль нее. Перенесем
в точку О силуF и, сложив с силой трения, получим силуF" .
Разложим силу F на продольнуюN и поперечнуюQ составляющие:
а поперечная Q – деформации сдвига и изгиба. Таким образом, зуб испытывает сложную деформацию. Анализ положения опасного сечения зуба показывает, что такое сечение в зубе находится на некотором расстоянииl x от точкиО и имеет ширину зуба в этом местеS z .
Напряжения сжатия малы по сравнению с напряжениями изгиба. Поэтому суммарные нормальные напряжения в опасном сечении зависят в основ-
Обычно расчет зуба ведут по той стороне зуба, на которой находят растянутые волокна, так как там быстрее появляются усталостные трещины. В этом случае зависимость (6.22) примет вид
ζ ζ изζ сж. | ||||
F тр | ||||
Oнапряжениями изгиба | ||||
S z 2 |
||||
Выразив силу F" через окружное усилиеF t , умножим числитель и знаменатель выражения (6.24) на модульm . Получим
F tK F | 6l x m cos α | m sin α | |||||||
cosα cos | |||||||||
S z cosα cos |
Выражение в скобках называется коэффициентом формы зуба и обозначается черезY F .
В окончательном виде формула для вычисления напряжений изгиба
в зубчатой передаче имеет вид
F β m | |||||||
где Y – коэффициент, учитывающий | изменение | изгибных напряжений |
|||||
в зависимости от угла наклона зуба; | |||||||
Y 1 β0 | |||||||
Коэффициент формы зуба | зависит от | числа зубьев колеса и |
коэффициента смещения исходного контура. Его величины приведены в таблицах или на графиках в справочной литературе. Приближенно значение Y F можно вычислить по формуле
Y F 3,6 1 2,8x 0,93Z v 112x 2 154x 71Z v 2 , (6.28)
где x – коэффициент смещения;Z v =Z /cos3 – приведенное (эквивалентное) число зубьев.
6. Особенности расчетов косозубых
и шевронных цилиндрических передач
На рис. 6.4, а приведена шевронная цилиндрическая передача, на рис. 6.4,б – схема косозубой передачи.
У косозубых и шевронных колес зубья располагаются не по образующей делительного цилиндра, а составляют с ней некоторый угол β (рис. 6.4).
Для нарезания косозубых зубьев используется тот же инструмент, что и для прямозубых колес. Поэтому профиль косого зуба в нормальном сечении n –n совпадает с профилем прямого зуба с соответствующим стандартным модулем.
В торцевом сечении параметры изменяются в зависимости от угла β: окружной шаг P t Р n / cos ;
окружной модуль m t m n / cos .
Индексы n иt соответствуют параметрам в нормальном и торцевом сечениях соответственно.
Прочность зуба зависит от его формы и размеров в нормальном сечении, что соответствует эквивалентному прямозубому колесу, которое имеет эквивалентный диаметр d v и эквивалентное число зубьевZ v :d v =d /cos2
и число зубьев Z v =Z /cos3 .
В отличие от прямых косые зубья входят в зацепление не сразу по всей длине, а постепенно, и в зацеплении находится, минимум, две пары зубьев. Это объясняет плавность работы косозубых колес, снижение шума и дополнительных динамических нагрузок. Рекомендуется угол наклона β = 8–20º, для шевронных колес β = 25–40º.
Силы в зацеплении. В косозубых передачах (рис. 6.5) между зубьями действует нормальная силаF n . Для удобства расчетов эту силу раскладывают
на три составляющие: окружную силу F t = 2T /d ; осевую силуF a =F t /tg ; радиальную силуF r F" t tgw F t tgw cos β.
ФЕДЕРАЛЬНОЕ АГЕНТСТВО ПО ОБРАЗОВАНИЮ
МОСКОВСКИЙ ГОСУДАРСТВЕННЫЙ ТЕХНИЧЕСКИЙ УНИВЕРСИТЕТ «МАМИ»
Кафедра «Детали машин и ПТУ»
РАСЧЕТ ЦИЛИНДРИЧЕСКИХ ЗУБЧАТЫХ ПЕРЕДАЧ
учебное пособие по дисциплине «Детали машин и основы конструирования» для студентов машиностроительных специальностей
МОСКВА – 2006
«Расчет цилиндрических зубчатых передач на прочность» учебное пособие по дисциплине «Детали машин и основы конструирования» для студентов машиностроительных специальностей.
Настоящее учебное пособие имеет целью дать студентам необходимые сведения для освоения методики расчета зубчатых передач по ГОСТ 21354-87. Оно является пособием при курсовом проектировании по дисциплине «Детали машин и основы конструирования» и другим профилирующим дисциплинам, а также можетт использоваться при выполнении дипломных проектов. В приложении дан пример выполнения расчетно-графической работы.
Размерность величин
Во всех расчетах принята размерность: размеры – мм; силы – Н; моменты – Н.м; напряжения – МПа;
скорость – м/c;
частота вращения – мин-1 (об/мин).
Индексация:
1 – величина, относящаяся к шестерне;
2 – величина, относящаяся к колесу;
Н – величины при расчете на контактные напряжения; F – величины при расчете на изгиб;
Б – быстроходная ступень; Т – тихоходная ступень.
1. Исходные данные для расчета ………………………………………………………………. 4
2. Проектировочный расчет по контактным напряжениям……………………………………4
2.1. Выбор материала зубчатых колес и их термообработки………………………………… 4
2. 2. Выбор точности изготовления колес………………………………………………...…... 4
2. 3. Выбор относительной ширины зубчатого венца………………………………………….6
2.4. Коэффициент, учитывающий неравномерность распределения нагрузки по длине контактных линий……………………………………………………………………………….6
2.5. Допускаемые контактные напряжения при расчете на сопротивление усталости……..7
2.6. Определение размеров зубчатой пары……………………………………………….…… 9
2.7. Размеры для контроля взаимного положения разноименных профилей…………….…15
2.8. Скорость и силы в зацеплении…………………………………………………………….16
2.9. Проверка заготовок колес на прокаливаемость…………………………………...…….. 16 3. Проверочный расчет по контактным напряжениям……………………………………… 17
3.1. Расчет на сопротивление усталости………………………………………………..……. 17
3.2. Расчет на контактную прочность при действии максимальной нагрузки………….…. 21 4. Проверочный расчет по напряжениям изгиба………………………………………………22
4.1. Расчет на сопротивление усталости………………………………………………….…...22
4.2. Расчет на прочность при действии максимальной нагрузки…………………………….27
5. Проектировочный расчет на сопротивление усталости при изгибе зуба………………...28 6. Особенности расчета некоторых передач………………………………………………….29
6.1. Шевронные передачи………………………………………………………………..…….29
6.2. Передачи многопоточных редукторов………………………………………………..…..29 6.3.Передачи с заданным межосевым расстоянием…………………………………….……30
6.4. Передачи соосного редуктора……………………………………………………………..32 Список литературы ………………………………………………………………..………….. 32
Приложение 1. Соотношение между твердостями HRC ,HB иHV ………………..…...33 Приложение 2. Типовые режимы нагружения…………………………………………….…33
Приложение 3. Пример расчета тихоходной косозубой цилиндрической зубчатой передачи соосного редуктора……………………………………………………………..…..34
Приложение 4. Пример расчета быстроходной косозубой цилиндрической зубчатой передачи соосного редуктора………………………………………………………………….45
1. ИСХОДНЫЕ ДАННЫЕ ДЛЯ РАСЧЕТА
Т 1 - момент на валу шестерни, Н.м;
Т 2 - момент на валу колеса, Н.м;
n 1 - частота вращения вала шестерни, мин–1 ; n 2 - частота вращения вала колеса, мин–1 ; u - передаточное число зубчатой передачи;
L h - срок службы в часах;
циклограмма нагружения или типовой режим нагружения; схема редуктора.
2. ПРОЕКТИРОВОЧНЫЙ РАСЧЕТ ПО КОНТАКТНЫМ НАПРЯЖЕНИЯМ
2.1. Выбор материала зубчатых колес и их термообработки
Материал колес и вид термообработки выбирают в зависимости от требований к
габаритам передачи и технологии изготовления.
Преимущественно применяют, стали с упрочненной рабочей поверхностью зубьев. При отсутствии жестких требований к размерам и малой мощности используют улучшенные или нормализованные стали.
В передачах с улучшенными колесами твёрдость шестерни следует делать выше твердости колеса из-за большей частоты её нагруженияH 1 ≈ H 2 + (25 ... 30 )HB . Это достигается выбором сталей разных марок или различием в термообработке при одной марке стали.
При колесах с поверхностным упрочнением твердость поверхностей зубьев шестерни и колеса делают одинаковой. Применяют также комбинацию шестерни с поверхностным упрочнением зубьев и улучшенным колесом. Выбор марки стали производится по табл.1.
На чертеже колеса (шестерни) в технических требованиях должны указываться пределы допустимого колебания твердости из расчета ± 15 HB * единиц от расчетной.
Пример . Если расчетная твердостьH = 300HB , на чертеже ставят твердость
285... 315HB .
Примечание. * Соотношение между твердостямиHRC ,HB иHV определяют по приложению 1.
2. 2. Выбор точности изготовления колес
Степень точности колес по плавности и контакту назначают по табл. 2 в зависимости от ожидаемой окружной скорости в зацеплении быстроходной пары редуктора.
Марки сталей, пределы выносливостиσ | , σ | Прочности [ σ ] | и коэффициенты S | ||||||||||||||||||||||||
Таблица 1 |
|||||||||||||||||||||||||||
Термическая | Твердость | σ H lim, | [σ ] | S F, | Y g, | Y d, |
|||||||||||||||||||||
обработка | Поверхности | Марка сталей | σ F lim | σ FSt | |||||||||||||||||||||||
Нормализация и | 180... 350HB | 40, 45, 40Х,40ХН, | 2 HB | 1, 75HB | 6, 5HB | ||||||||||||||||||||||
улучшение | 40ХФА,40ХН2МА | ||||||||||||||||||||||||||
Объемная закалка | 45 ...55 HRC | 40Х,40ХН,40ХН2МА | 2, 8σ Т | ||||||||||||||||||||||||
Сквозная закалка | 48 ...55 HRC | ||||||||||||||||||||||||||
при нагреве ТВЧ | |||||||||||||||||||||||||||
40ХН, 40ХН2МА | 17 HRC | ||||||||||||||||||||||||||
Закалка ТВЧ по | 48 ...58 HRC | 25... 35 | 40Х , 35ХМ, | ||||||||||||||||||||||||
контуру с охва- | |||||||||||||||||||||||||||
40ХН, 40ХН2МА | |||||||||||||||||||||||||||
том впадины | |||||||||||||||||||||||||||
Цементация с | 52 ...63 HRC | 18ХГТ ,30ХГТ , | |||||||||||||||||||||||||
автоматическим | |||||||||||||||||||||||||||
регулированием | |||||||||||||||||||||||||||
30... 45 | 20ХН, 20ХН2М , | 23 HRC | 44 HRC | ||||||||||||||||||||||||
процесса | |||||||||||||||||||||||||||
20ХН3А ,12ХН3А | |||||||||||||||||||||||||||
Цементация | 56 ...63 HRC | Всех марок | |||||||||||||||||||||||||
Нитроцементация | 57 ...63 HRC | 25ХГТ, 30ХГТ , | |||||||||||||||||||||||||
Азотирование | 700... 950HV | 24... 40 | 38Х2Ю, 38Х2МЮА | 290 + | |||||||||||||||||||||||
3 HV* | 12 HRC сердц | ||||||||||||||||||||||||||
550... 750HV | |||||||||||||||||||||||||||
Примечание. Наиболее применяемые марки сталей в автотракторостроении подчеркнуты.
* Соотношение между твердостями HRC ,HB иHV определяют по рис.1 приложения.
V ≈ | ||||||||
где n 1 - частота вращения шестерни;T 1 - вращающий момент на валу шестерни. | ||||||||
Таблица 2 |
||||||||
Для зубчатых колес | Степень точности при скорости V в м/с | |||||||
V ≤ 2 | 2 < V ≤ 4 | 4 < V ≤ 6 | 6 < V < 10 | 10 < V < 16 |
||||
прямозубых | ||||||||
косозубых и шевронных |
Примечание. В скобках указаны допустимые степени точности для малоответственных редукторов.
2. 3. Выбор коэффициента относительной ширины зубчатого венца
Коэффициент относительной ширины зубчатого венца рекомендуют выбирать в пределах, указанных в табл. 3.
Коэффициент относительной ширины зубчатого венца
Таблица 3 |
|||||||||
При степени точности | |||||||||
при H 2 < 350 HB | |||||||||
при H2 > 40HRC | |||||||||
Большие значения для косозубых колес при симметричном расположении относительно опор и постоянной нагрузке, когда обеспечивается более равномерное распределение нагрузки по ширине колес и возможна приработка. Для коробок передач ψ bd = 0 , 15 ... 0 , 4 .
При консольном расположении хотя бы одного из колес ψ bd = 0 , 5 ... 0 , 8 . Для открытых передачψ bd = (10 ... 12 ) / z 1 .
2.4. Коэффициент, учитывающий неравномерность распределения нагрузки по длине контактных линий
Коэффициент K H β - определяют по рис. 1 в зависимости от твердости поверхности зубьев, коэффициента относительной ширины зубчатого венцаψ bd и расположения колес относительно опор валов.
При уточненном расчёте K H β находят по ГОСТ 21354-87 с учётом упругой линии вала, зазоров в подшипниках и жесткостей зубьев.
Коэффициент K H β
0,5b |
|||||
К Hb | при H B 1 < 350 илиH B 2 < 350 | К H b при H B1 > 350 и H B2> 350 |
||||
y bd | 0,8 1,2 y bd |
|||||
2.5. Допускаемые контактные напряжения при расчете на сопротивление усталости
Определяют раздельно для шестерни и колеса по формуле
[σ ] | σ H lim Z N Z | |||||||
Примечание. При проектировочном расчете передач общего назначения принимают
Z RZ VZ X= 0 , 9 .
За расчетное допускаемое контактное напряжение принимают соответственно меньшее из двух:
для прямозубых передач [ σ ] H 1 или[ σ ] H 2 ;
для косозубых и шевронных передач
[ σ ] H= 0 , 45 ([ σ ] H1 + [ σ ] H2 ) , или [ σ ] H= 1 , 25 [ σ ] H min. | ||
2.5.1. Предел контактной выносливости σ H lim находят по формулам - табл.1. При |
||
этом расчет | ведут по средней твердости HB илиHRC . Для улучшенных | |
указанном в | таблице интервале твердости (180 ... 350 )HB в зависимости от требуемых |
габаритов для расчета может быть взята любая твердость.
2.5.2. Коэффициент запаса прочности: для колес улучшенных и объемно-закаленных |
||
S H = 1 , 1 (1 , 25 ) ; для колес с поверхностным упрочнениемS H = 1 , 2 (1 , 35 ) . Значения в |
||
скобках - для особо ответственных передач. | ||
2.5.3. Коэффициенты долговечности | ||
При N HE≤ N HG, | Z N 1 = 6 N HG, | |
а при N HE > N HG -Z N 2 = 20 N HG ≥ 0 , 75 . | ||
Для колес улучшенных и объемно-закаленных Z N ≤ 2 , 6 ; с поверхностным упрочнением |
||
Z N ≤ 1, 8. | ||
2.5.3.1. Базовое число циклов по формуле | ||
N HG = 30 HB2 ,4 ≈ 340 HRC3,15 + 8 106 ≤ 120 106 . |
2.5.3.2. Суммарные числа циклов нагружения за период службы для шестерни N Σ 1
и колеса N Σ 2 определяются:
Здесь n зац - число зацеплений одной стороны зуба за один оборот шестерни или колеса;t i
Время работы на скоростном режиме n i на протяжении суток, в часах;n - частота вращения рассматриваемого зубчатого колеса;д - число рабочих дней в году;л - срок службы передачи, в годах;t с - время работы на протяжении суток, в часах;L h = t с д л
Ресурс работы передачи в часах.
Примечание. Если для шестерни и колесаn зац = 1 , тоN Σ 2 = N Σ 1 / u , гдеu -
передаточное число передачи.
2.5.3.3.Коэффициент режима работы При заданной циклограмме нагружения и различной частоте вращения на каждой
ступени нагружения коэффициент режима работы находят по формуле
µ H =µ 3 = | ∑n | |||||
∑ n it i |
при n= const
= µ | |||||||||||
где n i ,t i ,T i - частота вращения, время работы и вращающий момент наi − й ступени нагружения;T max - наибольший длительно действующий момент, длительность действия которого за срок службы не менее0 , 03 N HG циклов;t i / t Σ - относительное время работы наi − й ступени нагружения;t Σ - суммарное время работы.
Моменты, действующие за срок службы менее 0 , 03 N HG циклов, при расчете на сопротивление усталости не учитываются.
Если циклограмма нагружения соответствует типовому режиму нагружения, то
Примечание. Если для шестерни и колесаn зац = 1 , тоN HE 2 = N HE 1 / u .
2.5.4. Коэффициент, учитывающий влияние исходной шероховатости поверхностей
зубьев Z R принимают: | |||
Шероховатость, мкм | Ra = 1 ,25 ...0 ,63 | Ra = 2 ,5 ...1 ,25 | RZ = 40 ...10 |
0, 95 |
2.5.5. Коэффициент, учитывающий влияние окружной скорости Z V - по рис.2. 2.5.6. Коэффициент, учитывающий размеры зубчатого колесаZ X - по рис.3, в
зависимости от диаметра d колеса.
2.6. Определение размеров зубчатой пары
2.6.1. Начальный диаметр шестерни по формуле
наибольший момент на колесе, длительность действия которого за срок службы не менее
50000 циклов; ψ bd назначают согласно п. 2.3.;K H β - по п. 2.4. Определение[ σ ] H по п.
Знак «+» соответствует внешнему зацеплению колес, «-» - внутреннему.
Коэффициент Z V | Коэффициент Z X | |||||||||||
200 400 600 800 d W , мм | ||||||||||||
16 18 V, м/c | ||||||||||||
2.6.2. По найденному диаметру d w 1 определяют: | ||||||||||||
расчетную ширину колес | b расч. | |||||||||||
расчетное межосевое расстояние a w расч. = d w 1 (u + 1 ) , | ||||||||||||
которое округляют по табл. 4 до стандартного. Ряд 1 следует предпочитать ряду 2. | ||||||||||||
Примечание. В обоснованных случаях межосевое расстояние может быть не |
||||||||||||
стандартным. | ||||||||||||
Стандартные межосевые расстояния a w в мм | ||||||||||||
Таблица 4 |
В случае существенного изменения a w корректируют ширину колеса | |||||||||||||||||||||||||||||||
a расч. 2 | |||||||||||||||||||||||||||||||
b треб.= b расч. | |||||||||||||||||||||||||||||||
Ширина колеса b | B треб. ; ширина шестерни | + (5 ... 8 ) мм. С округлением |
|||||||||||||||||||||||||||||
до целого числа. | |||||||||||||||||||||||||||||||
2.6.3. Определение геометрии зацепления | |||||||||||||||||||||||||||||||
2.6.3.1. При колесах с твердостью поверхности зубьев колеса HB 2 ≤ 350 | |||||||||||||||||||||||||||||||
Задаются по табл. 5 | модулем в пределах: m ≈ (0 , 01 ... 0 , 02 ) a w ≥ 1 , 5 мм. При |
большей твердости зубьев шестерни - по верхнему пределу. Для силовых передач следует брать модуль не менее 1,5 мм. Ряд 1 следует предпочитать ряду 2.